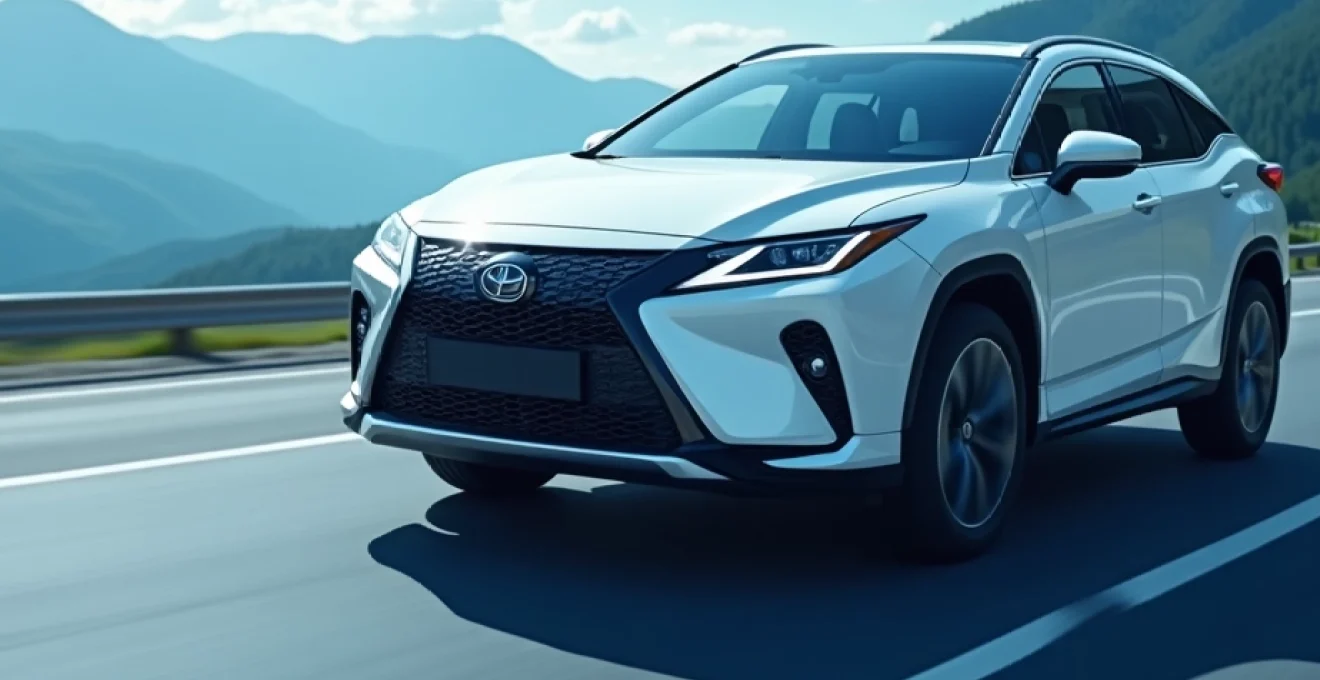
The automotive industry is undergoing a profound transformation, driven by the urgent need to reduce carbon emissions and embrace sustainable technologies. Alternative energies are at the forefront of this revolution, reshaping how vehicles are powered, designed, and manufactured. From electric powertrains to hydrogen fuel cells, biofuels to solar integration, these innovative technologies are not just changing the cars we drive—they're redefining the entire automotive ecosystem.
As you navigate this shifting landscape, understanding the impact of alternative energies on the auto industry becomes crucial. Whether you're a consumer, industry professional, or policymaker, the decisions made today will shape the future of transportation for generations to come.
Electric vehicle powertrain technologies: battery and motor advancements
The heart of the electric vehicle (EV) revolution lies in its powertrain—the combination of batteries and electric motors that propel these vehicles forward. Recent advancements in battery technology have been nothing short of remarkable. Lithium-ion batteries, the current standard, have seen significant improvements in energy density, allowing EVs to travel further on a single charge.
One of the most exciting developments is the emergence of solid-state batteries. These next-generation power sources promise even higher energy densities, faster charging times, and improved safety compared to their liquid electrolyte counterparts. Companies like QuantumScape and Toyota are investing heavily in this technology, with the potential to revolutionize EV range and performance.
Electric motors have also seen substantial advancements. The shift towards permanent magnet synchronous motors (PMSMs) has improved efficiency and power density. Additionally, the development of axial flux motors offers even greater power-to-weight ratios, potentially changing the game for electric vehicle performance.
Innovations in power electronics, such as silicon carbide (SiC) semiconductors, are enabling more efficient power conversion and management within EVs. These advancements not only improve overall vehicle efficiency but also contribute to reduced charging times and extended range.
Hydrogen fuel cell vehicles: infrastructure and performance analysis
While battery electric vehicles dominate the alternative energy conversation, hydrogen fuel cell vehicles (FCEVs) offer a compelling alternative, especially for long-range and heavy-duty applications. FCEVs combine the zero-emission benefits of electric vehicles with the quick refueling times of conventional cars, making them an attractive option for certain use cases.
However, the widespread adoption of FCEVs faces significant challenges, primarily related to infrastructure. The lack of a comprehensive hydrogen refueling network remains a major hurdle. As of 2023, there are only about 107 public hydrogen fueling stations in the United States, with the majority concentrated in California.
Toyota Mirai and Honda Clarity: case studies in FCEV technology
Two prominent examples of consumer FCEVs are the Toyota Mirai and Honda Clarity. These vehicles showcase the potential of fuel cell technology in passenger cars. The second-generation Toyota Mirai, for instance, boasts a range of up to 402 miles on a single tank of hydrogen, demonstrating the long-range capabilities of FCEVs.
The Honda Clarity Fuel Cell, while discontinued in 2021, provided valuable insights into FCEV technology and consumer adoption. Both vehicles highlighted the smooth, quiet operation characteristic of electric powertrains, combined with the quick refueling times of conventional vehicles.
Hydrogen production methods: steam reforming vs. electrolysis
The environmental impact of FCEVs heavily depends on how the hydrogen fuel is produced. Currently, the most common method is steam methane reforming, which uses natural gas as a feedstock. While this process is cost-effective, it still results in carbon emissions.
Electrolysis, on the other hand, offers a potentially zero-emission pathway for hydrogen production. By using renewable electricity to split water into hydrogen and oxygen, this method could provide truly clean hydrogen fuel. However, the costs associated with electrolysis remain higher than steam reforming, presenting an economic challenge for widespread adoption.
Challenges in hydrogen storage and distribution networks
Storing and distributing hydrogen presents unique challenges due to its low density and high flammability. Compressed hydrogen tanks in vehicles must be engineered to withstand high pressures while remaining lightweight. The distribution infrastructure requires specialized pipelines and storage facilities, adding complexity and cost to the FCEV ecosystem.
Despite these challenges, several countries, including Japan and Germany, are investing heavily in hydrogen infrastructure. These efforts could pave the way for more widespread FCEV adoption in the coming years.
Fuel cell efficiency: PEM vs. SOFC technologies
Two primary types of fuel cells are being developed for automotive applications: Proton Exchange Membrane (PEM) and Solid Oxide Fuel Cells (SOFC). PEM fuel cells are currently the standard for automotive use due to their lower operating temperatures and quick start-up times.
SOFCs, while less common in vehicles, offer higher electrical efficiency and the ability to use a wider range of fuels. However, their high operating temperatures and longer start-up times have limited their application in automobiles. Ongoing research aims to overcome these limitations, potentially expanding the role of SOFCs in future vehicle designs.
Biofuels in the automotive sector: ethanol and biodiesel applications
Biofuels represent another significant alternative energy source in the automotive industry, offering a renewable option for internal combustion engines. Ethanol and biodiesel are the two most common biofuels used in vehicles today, each with its own set of advantages and challenges.
Ethanol, primarily derived from corn in the United States, is commonly blended with gasoline. E10 (10% ethanol, 90% gasoline) is widely available, while higher blends like E85 are used in flex-fuel vehicles. Ethanol production has become more efficient over the years, with advanced processes reducing its carbon footprint.
Biodiesel, produced from vegetable oils or animal fats, can be used in many diesel engines with little or no modification. It's often blended with petroleum diesel, with B20 (20% biodiesel) being a common mix. Biodiesel offers lower emissions compared to conventional diesel and can be produced from a variety of feedstocks, including waste cooking oil.
The use of biofuels faces several challenges, including land use concerns, potential competition with food crops, and variations in fuel quality. However, advanced biofuels made from non-food biomass, such as agricultural waste or algae, show promise in addressing some of these issues.
Solar-powered vehicles: photovoltaic integration and energy management
While solar power alone cannot yet fully power a conventional passenger vehicle, integrating photovoltaic (PV) cells into vehicles offers exciting possibilities for supplementing battery power and extending range. Solar panels on vehicles can help charge the battery during parking or driving, potentially adding several miles of range per day.
Sono Sion: analyzing the first mass-produced solar electric vehicle
The Sono Sion represents a significant milestone in solar vehicle technology. This compact car features integrated solar cells across its body, capable of adding up to 70 miles of range per week under optimal conditions. While not sufficient to eliminate the need for plug-in charging, this solar integration demonstrates the potential for reducing reliance on the grid and extending the practical range of EVs.
The Sion's design highlights the challenges and opportunities in solar vehicle integration, including optimizing panel placement, managing heat, and balancing aesthetics with functionality.
Thin-film solar cells vs. Crystalline silicon for vehicle integration
The choice of solar cell technology significantly impacts the effectiveness of vehicle-integrated photovoltaics. Crystalline silicon cells offer higher efficiency but are rigid and more challenging to integrate into vehicle designs. Thin-film solar cells, while less efficient, provide greater flexibility in terms of shape and placement.
Emerging technologies like perovskite solar cells show promise for vehicle integration, offering potentially higher efficiencies in a flexible format. As these technologies mature, we may see more creative and effective solar integration in future vehicle designs.
Maximum Power Point Tracking (MPPT) in automotive solar systems
Maximizing the power output from vehicle-integrated solar panels requires sophisticated energy management systems. Maximum Power Point Tracking (MPPT) technology plays a crucial role in this process. MPPT controllers continuously adjust the electrical operating point of the solar array to extract the maximum possible power under varying conditions.
In automotive applications, MPPT systems must be particularly robust to handle the rapidly changing light conditions experienced during driving. Advanced algorithms and fast-responding hardware are essential for capturing as much solar energy as possible.
Challenges in solar vehicle aerodynamics and weight distribution
Integrating solar panels into vehicle design presents unique challenges in terms of aerodynamics and weight distribution. The placement of solar cells can affect the vehicle's drag coefficient, potentially impacting range and efficiency. Engineers must balance the benefits of solar power generation with the need for optimal aerodynamic performance.
Weight distribution is another critical consideration. Adding solar panels and associated electronics increases the vehicle's overall weight and can affect handling characteristics. Clever design solutions, such as using the solar panels as structural elements, can help mitigate these challenges.
Hybrid powertrains: combining conventional and alternative energy sources
Hybrid powertrains represent a bridge between conventional internal combustion engines and fully electric vehicles. By combining multiple energy sources, hybrid vehicles offer improved fuel efficiency and reduced emissions while maintaining the range and convenience of traditional cars.
The most common hybrid configuration is the parallel hybrid, where both the electric motor and gasoline engine can drive the wheels. Series hybrids, where the gasoline engine serves only as a generator to charge the battery, offer another approach. Plug-in hybrid electric vehicles (PHEVs) add the ability to charge the battery from an external power source, further reducing reliance on fossil fuels.
Advanced hybrid systems are increasingly incorporating regenerative braking, which captures energy typically lost during deceleration and converts it back into electricity. This technology significantly improves overall efficiency, especially in urban driving conditions.
The future of hybrid powertrains may include more diverse energy sources. For example, some researchers are exploring the possibility of combining hydrogen fuel cells with batteries, offering the benefits of both technologies in a single vehicle.
Alternative energy impact on auto manufacturing and supply chains
The shift towards alternative energy vehicles is having a profound impact on automotive manufacturing processes and supply chains. Traditional assembly lines optimized for internal combustion engines are being retooled to accommodate the unique requirements of electric and hybrid powertrains.
Lithium-ion battery production: raw material sourcing and recycling
The production of lithium-ion batteries has become a critical component of the EV supply chain. Sourcing raw materials like lithium, cobalt, and nickel presents both economic and ethical challenges. Many automakers are working to secure stable supply chains for these materials while also addressing concerns about environmental impact and labor practices.
Battery recycling is emerging as a crucial industry to address the end-of-life issues associated with EV batteries. Companies are developing new processes to recover valuable materials from used batteries, creating a more circular economy for EV production.
Retooling assembly lines: ICE to EV manufacturing transition
The transition from internal combustion engine (ICE) to EV production requires significant changes in manufacturing processes. Assembly lines must be reconfigured to handle the installation of large battery packs, electric motors, and power electronics. This transition often involves substantial investment in new equipment and workforce training.
Automakers are also exploring more flexible manufacturing strategies that allow them to produce both ICE and EV models on the same production lines, providing adaptability during the transition period.
Rare earth elements in electric motors: supply challenges and alternatives
Many electric motors rely on rare earth elements, particularly neodymium and dysprosium, for their powerful permanent magnets. The limited global supply of these elements, dominated by a few countries, has raised concerns about potential shortages and price volatility.
In response, researchers and manufacturers are exploring alternative motor designs that reduce or eliminate the need for rare earth elements. Innovations in switched reluctance motors and induction motors show promise in this area, potentially offering more sustainable and geopolitically stable options for EV powertrains.
Carbon fiber and lightweight materials in alternative energy vehicles
The push for greater efficiency in alternative energy vehicles has led to increased use of lightweight materials like carbon fiber reinforced polymers (CFRP). These materials offer significant weight savings compared to traditional steel, improving range and performance.
However, the production of carbon fiber is energy-intensive and currently relies heavily on fossil fuels. Researchers are exploring more sustainable production methods, including the use of renewable energy in manufacturing processes and the development of bio-based carbon fibers.
The integration of these advanced materials into vehicle designs presents new challenges for manufacturing and recycling. Automakers are developing innovative joining techniques and exploring ways to make carbon fiber components more recyclable at the end of a vehicle's life.