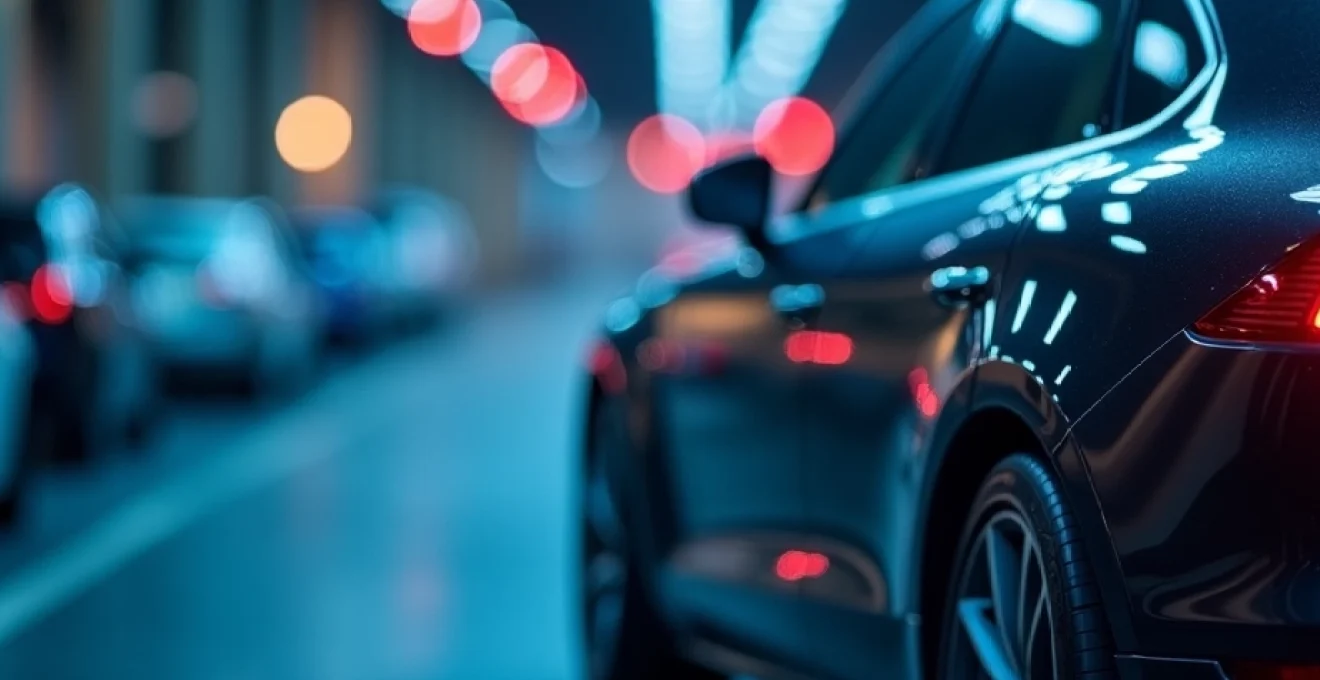
In the realm of modern automotive technology, electronic systems have become the backbone of vehicle performance, safety, and comfort. As cars evolve into sophisticated machines driven by intricate networks of sensors, processors, and actuators, the importance of proper electronic system maintenance cannot be overstated. From ensuring optimal engine performance to safeguarding advanced driver assistance features, a well-maintained electronic infrastructure is crucial for a smooth and safe ride.
The complexity of today's vehicles demands a comprehensive approach to maintenance that goes beyond traditional mechanical upkeep. As drivers and vehicle owners, understanding the fundamentals of electronic system care is essential for maximizing the longevity and reliability of our automotive investments.
Electronic control units (ECUs) in modern vehicles
At the heart of a modern vehicle's electronic system lies a network of Electronic Control Units (ECUs). These sophisticated computers are responsible for managing various vehicle functions, from engine performance and transmission control to climate systems and infotainment interfaces. The average luxury vehicle today can contain upwards of 100 ECUs, each dedicated to specific tasks and communicating with one another via complex data networks.
ECUs continuously monitor and adjust vehicle parameters based on input from an array of sensors. For instance, the Engine Control Module (ECM) processes data from oxygen sensors, mass airflow sensors, and throttle position sensors to optimize fuel injection and ignition timing. This real-time adjustment ensures optimal performance, fuel efficiency, and emissions control.
Maintaining these ECUs is crucial for several reasons:
- Ensuring accurate sensor readings and actuator responses
- Preventing communication errors between different systems
- Safeguarding against software glitches and vulnerabilities
- Extending the lifespan of electronic components
Regular diagnostic checks using specialized equipment can help identify potential issues before they escalate into major problems. These checks often involve scanning for Diagnostic Trouble Codes (DTCs), which we'll explore in the next section.
Diagnostic trouble codes (DTCs) and OBD-II systems
One of the most significant advancements in vehicle diagnostics came with the introduction of On-Board Diagnostics II (OBD-II) systems. This standardized system allows technicians and vehicle owners to access vital information about a vehicle's health through Diagnostic Trouble Codes (DTCs). When an ECU detects an anomaly or malfunction, it generates a specific DTC, which can be retrieved using an OBD-II scanner.
Understanding and interpreting these codes is a crucial aspect of electronic system maintenance. While some codes may indicate minor issues, others can signal serious problems that require immediate attention. Let's examine some common DTCs across different vehicle systems.
Common DTCs in engine management systems
Engine-related DTCs often start with the letter "P" (for Powertrain) and can indicate a wide range of issues. Some frequently encountered codes include:
- P0300-P0308: Cylinder misfire detected
- P0171-P0175: Fuel system too lean or rich
- P0401-P0408: Exhaust Gas Recirculation (EGR) system malfunction
These codes can point to problems ranging from faulty spark plugs and oxygen sensors to more complex issues with the EGR valve or fuel injectors. Regular scanning for these codes, even when no apparent issues are present, can help catch problems early and prevent more severe engine damage.
Transmission Control Module (TCM) fault codes
The Transmission Control Module manages the intricate processes of gear shifting and torque conversion. DTCs related to transmission issues often indicate problems with shift solenoids, speed sensors, or internal mechanical components. Common transmission-related codes include:
- P0700: Transmission Control System Malfunction
- P0715: Input/Turbine Speed Sensor Circuit Malfunction
- P0730-P0736: Gear ratio incorrect for specific gears
Addressing these codes promptly can prevent catastrophic transmission failure and costly repairs. Regular transmission fluid checks and changes, as recommended by the vehicle manufacturer, can also help prevent many TCM-related issues.
Interpreting ABS and traction control DTCs
Anti-lock Braking Systems (ABS) and Traction Control Systems play a critical role in vehicle safety. DTCs related to these systems often start with "C" (for Chassis) and can indicate problems with wheel speed sensors, hydraulic pumps, or control modules. Some examples include:
- C0035-C0038: Left/Right Front/Rear Wheel Speed Sensor Circuit Malfunction
- C0121: Valve Relay Circuit Malfunction
- C0200: Vehicle Speed Sensor Circuit Malfunction
Ignoring these codes can compromise vehicle stability and braking performance, especially in emergency situations. Regular brake system inspections, including sensor cleaning and wiring checks, can help prevent many ABS and traction control issues.
Preventive maintenance of vehicle electronics
While reactive maintenance in response to DTCs is important, a proactive approach to electronic system care can prevent many issues from occurring in the first place. Preventive maintenance of vehicle electronics involves several key areas of focus.
Battery health and alternator performance checks
The health of a vehicle's electrical system starts with its power source. Regular battery and alternator checks are crucial for maintaining the stability of the entire electronic infrastructure. A weak battery or failing alternator can lead to erratic behavior in various electronic systems, from intermittent sensor failures to complete ECU shutdowns.
To ensure optimal battery health:
- Test battery voltage and capacity regularly, especially before extreme weather seasons
- Clean battery terminals and check for corrosion
- Ensure proper electrolyte levels in non-sealed batteries
- Replace batteries proactively based on manufacturer recommendations
Alternator performance should be checked annually or whenever battery issues are suspected. A properly functioning alternator should maintain a charging voltage between 13.5 and 14.5 volts under normal operating conditions.
Cleaning and protecting ECU connectors
The integrity of electrical connections is paramount in maintaining reliable electronic system performance. Over time, connectors can accumulate dirt, moisture, or corrosion, leading to intermittent failures or erroneous sensor readings. Regular inspection and cleaning of ECU connectors can prevent many electronic gremlins from surfacing.
When cleaning connectors:
- Disconnect the battery to prevent short circuits
- Use electronic contact cleaner spray to remove debris and moisture
- Apply dielectric grease to protect against future contamination
- Ensure connectors are fully seated and secured after cleaning
Special attention should be given to connectors in areas prone to water exposure or heat accumulation, as these environments can accelerate connector degradation.
Software updates and ECU reprogramming
Just as our smartphones and computers require regular software updates, vehicle ECUs often benefit from firmware upgrades. These updates can address known issues, improve performance, and even enhance fuel efficiency. Many modern vehicles support over-the-air (OTA) updates, but others may require a visit to a dealership or specialized service center.
It's important to stay informed about available updates for your vehicle's ECUs. Manufacturers often release technical service bulletins (TSBs) that detail software improvements or fixes for specific issues. Regular checkups with authorized service providers can ensure your vehicle's electronic systems are running the latest and most optimized software versions.
Sensor calibration and replacement schedules
The accuracy of sensor data is critical for proper ECU function. Over time, sensors can drift out of calibration or fail entirely. While some sensors are designed to last the lifetime of the vehicle, others have recommended replacement intervals. Oxygen sensors, for example, typically require replacement every 60,000 to 100,000 miles, depending on the vehicle model and driving conditions.
Regular sensor calibration checks can help identify potential issues before they affect vehicle performance. Some sensors that may require periodic calibration or replacement include:
- Mass airflow sensors
- Throttle position sensors
- Camshaft and crankshaft position sensors
- Manifold absolute pressure sensors
Adhering to manufacturer-recommended replacement schedules and performing calibration checks during routine service can prevent many sensor-related issues and ensure optimal engine performance.
Advanced driver assistance systems (ADAS) maintenance
As vehicles become increasingly autonomous, the maintenance of Advanced Driver Assistance Systems (ADAS) has become a critical aspect of electronic system care. These systems rely on a complex network of sensors, cameras, and radar units to provide features like adaptive cruise control, lane-keeping assistance, and automatic emergency braking.
Camera and radar sensor alignment procedures
The precision of ADAS features depends heavily on the proper alignment of cameras and radar sensors. Even minor misalignments can lead to false positives or reduced effectiveness of safety systems. Alignment procedures should be performed after any front-end collision, windshield replacement, or suspension work that might affect the vehicle's geometry.
Alignment procedures typically involve:
- Placing calibration targets at specific distances from the vehicle
- Using specialized diagnostic equipment to adjust sensor angles
- Performing dynamic calibration through test drives
- Verifying system functionality through real-world scenario testing
It's crucial to note that ADAS calibration often requires specialized equipment and training, making it a task best left to qualified technicians with the proper tools and expertise.
Lidar system calibration for autonomous features
As vehicles move towards higher levels of autonomy, LiDAR (Light Detection and Ranging) systems are becoming more prevalent. These systems provide high-resolution 3D mapping of the vehicle's surroundings, crucial for advanced autonomous features. LiDAR calibration is a complex process that ensures accurate distance measurements and object detection.
LiDAR calibration typically involves:
- Geometric calibration to align LiDAR data with the vehicle's coordinate system
- Intensity calibration to ensure consistent object recognition across different surfaces
- Multi-sensor fusion calibration to integrate LiDAR data with other sensor inputs
Regular LiDAR system checks and calibrations are essential for maintaining the reliability of autonomous driving features and ensuring passenger safety.
Maintaining GPS and navigation system accuracy
While often taken for granted, the accuracy of GPS and navigation systems is crucial for many modern vehicle features, from basic route guidance to advanced geofencing capabilities in fleet management systems. Maintaining these systems involves both hardware and software considerations.
To ensure optimal GPS performance:
- Keep GPS antenna areas clear of obstructions and debris
- Regularly update navigation system maps and software
- Check for and address any electromagnetic interference issues
- Verify the accuracy of the vehicle's internal clock, which can affect GPS calculations
For vehicles equipped with high-precision GPS for autonomous or semi-autonomous operation, professional calibration and verification may be necessary to maintain centimeter-level accuracy.
Cybersecurity in vehicle electronic systems
As vehicles become more connected and reliant on electronic systems, cybersecurity has emerged as a critical concern in automotive maintenance. Protecting vehicle electronic systems from potential cyber threats is not just about preventing data breaches; it's about ensuring the safety and reliability of the vehicle itself.
Over-the-Air (OTA) update security protocols
Over-the-Air updates have revolutionized the way vehicle software is maintained, allowing manufacturers to quickly deploy fixes and improvements. However, this convenience also introduces potential security vulnerabilities. Robust security protocols for OTA updates are essential to prevent malicious actors from injecting harmful code into vehicle systems.
Key security measures for OTA updates include:
- Strong encryption for update packages
- Secure authentication mechanisms for update servers
- Integrity checks to verify the authenticity of updates
- Rollback capabilities in case of update failures or security breaches
Vehicle owners should ensure that their vehicles are connected to secure networks when receiving updates and follow manufacturer guidelines for update procedures to minimize security risks.
CAN bus network protection strategies
The Controller Area Network (CAN) bus is the primary communication network for most vehicle electronic systems. While efficient and reliable, the CAN bus was not initially designed with strong security features, making it a potential target for cyber attacks. Protecting the CAN bus is crucial for maintaining the integrity of vehicle electronic systems.
Protection strategies for CAN bus networks include:
- Implementing message authentication codes (MACs) to verify the authenticity of CAN messages
- Using firewalls to segregate critical systems from potentially vulnerable external interfaces
- Employing intrusion detection systems to identify and alert on suspicious network activity
- Regular security audits and penetration testing of vehicle networks
As vehicles become more connected, the importance of securing internal networks against potential intrusions cannot be overstated.
Telematics and infotainment system vulnerability management
Telematics and infotainment systems often serve as the primary interface between the vehicle's internal networks and external connections, making them potential entry points for cyber attacks. Managing vulnerabilities in these systems is crucial for overall vehicle security.
Key aspects of vulnerability management include:
- Regular security patching of infotainment system software
- Implementing strong access controls for telematics services
- Conducting periodic vulnerability assessments of connected services
- Educating vehicle owners about safe practices when using connected features
Manufacturers and service providers must work together to ensure that these systems remain secure throughout the vehicle's lifecycle, with ongoing support and updates to address emerging threats.
Future trends in automotive electronic maintenance
As we look towards the future of automotive technology, several trends are shaping the landscape of electronic system maintenance. These advancements promise to make vehicles more reliable, efficient, and easier to maintain, but they also bring new challenges for technicians and vehicle owners alike.
One significant trend is the increasing use of artificial intelligence (AI) and machine learning in vehicle diagnostics. These technologies enable predictive maintenance by analyzing vast amounts of sensor data to identify potential issues before they manifest as failures. AI-driven diagnostics can potentially reduce downtime and maintenance costs by allowing for more targeted and timely interventions.
Another emerging trend is the integration of blockchain technology for secure record-keeping of vehicle maintenance and software updates. This could provide an immutable record of a vehicle's service history, enhancing transparency and trust in the used car market while also ensuring the integrity of critical safety and performance updates.
The rise of electric vehicles (EVs) is also reshaping maintenance paradigms. With fewer moving parts and a focus on battery health, EV maintenance routines differ significantly from those of traditional internal combustion engines. As EVs become more prevalent, technicians will need to adapt their skills to focus more on high-voltage systems, battery diagnostics, and power electronics maintenance.
Augmented reality (AR) is poised to revolutionize maintenance procedures by providing technicians with real-time, visual guidance for complex tasks. AR systems can overlay diagnostic information and step-by-step instructions directly onto the technician's view of the vehicle, potentially reducing errors and improving efficiency in maintenance operations.
As vehicles continue to evolve towards higher levels of autonomy, the complexity of electronic systems will increase exponentially. This will necessitate a shift in maintenance strategies, focusing more on software and sensor calibration than traditional mechanical adjustments. Predictive maintenance algorithms will likely become more sophisticated, leveraging big data analytics to forecast potential failures with greater accuracy.
The integration of vehicle-to-everything (V2X) communication will also impact maintenance practices. As vehicles become more connected to infrastructure and other vehicles, maintaining the integrity and security of these communication systems will be crucial. This may involve regular software updates and security patches to protect against evolving cyber threats.
Furthermore, the concept of "right to repair" is gaining traction, potentially leading to more open access to diagnostic information and repair procedures. This could democratize vehicle maintenance, allowing for a wider range of service options for vehicle owners. However, it also raises concerns about maintaining the security and integrity of increasingly complex vehicle systems.
As we move towards a more sustainable automotive future, the recyclability and environmental impact of electronic components will become a more significant consideration in maintenance practices. This may lead to the development of more modular electronic systems that are easier to repair, upgrade, or recycle, reducing the overall environmental footprint of vehicle maintenance.